DESIGN WITH IMPLEMENTATION IN MIND
Good engineering design takes a holistic approach to problem solving; considering part manufacturability and compatibility with other components in the system. This approach ensures that the parts we design not only meet your specifications but also seamlessly integrate into the manufacturing process. Integrating our manufacturing knowledge into the design stage allows us to optimize the functionality and performance of your parts, creating high-quality end products that excel in fit, form and function.
DESIGNING WITH ADVANCED MATERIALS
Material selection plays a critical role in part design, and we approach it with meticulous attention. Whether you are designing a final or prototype part, we can carefully select and utilize materials that align with the design objectives.
- Advanced materials offer enhanced properties such as strength, durability, and lightweight characteristics.
- Prototype materials allow for quick iterations and extensive testing.
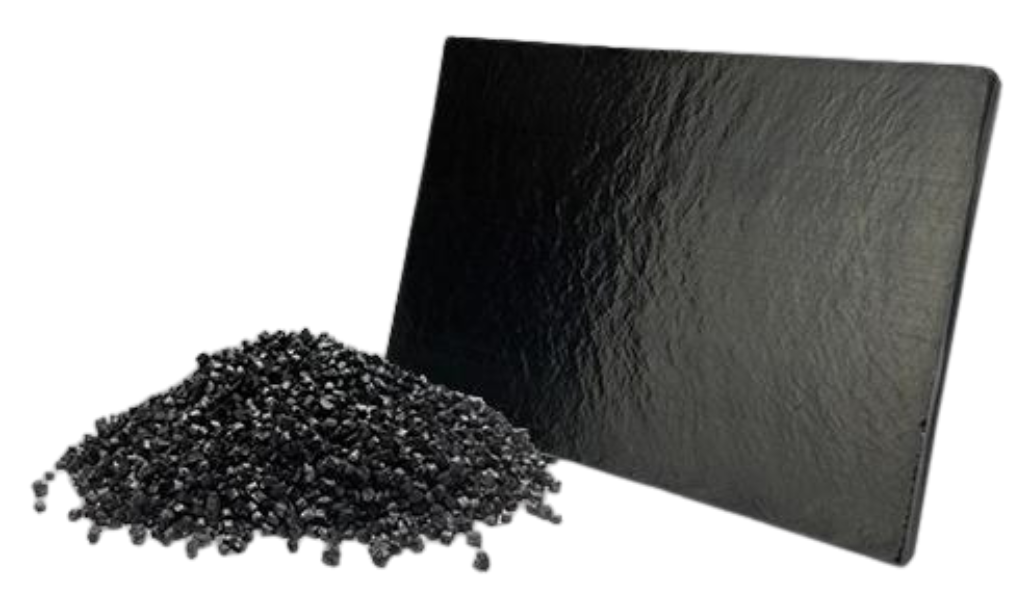
PART EVALUATION WITH MOLD FLOW ANALYSIS
Part evaluation is a fundamental part of our engineering process. Alpine engineers utilize techniques such as mold flow analysis (MFA) to assess the manufacturability of designed parts to optimize cycle time and keep scrap rates low.
Mold flow analysis is an advanced simulation method that predicts and optimizes the flow of materials through the mold during injection molding (IM) with a high degree of accuracy. By subjecting the design to this analysis, our engineers can mitigate potential IM risks such as warping and air traps, avoid costly tooling modifications, and ensure the part will meet performance specifications.
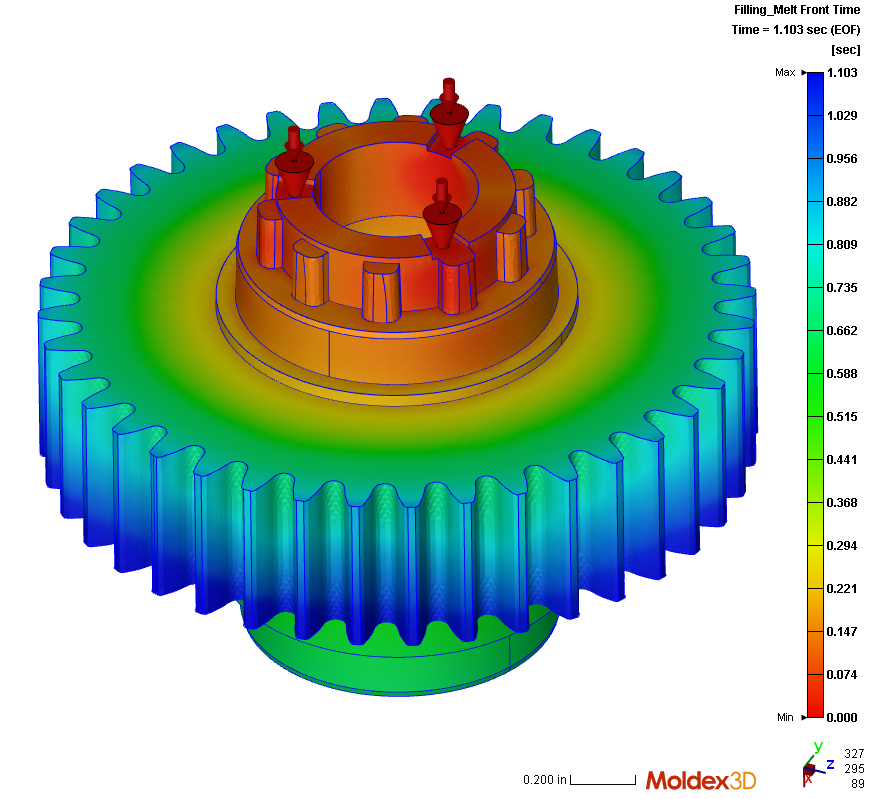
Benefits of Mold Flow Analysis
Mold flow analysis ensures a smooth transition to the production stage. This process helps to:
- Identify and mitigate potential risks early in the design stage, such as warping, shrinkage, and air traps.
- Test various gating, cooling, and pressure scenarios to observe moldability options.
- Avoid costly and time-consuming tooling modifications.
- Address performance considerations during the design phase when coupled with Finite Element Analysis (FEA).
- Anticipate production requirements before the tooling process begins.
Leveraging the insights gained from mold flow analysis enhances the overall performance and productibility of the parts, ensuring that they meet the highest standards of excellence. In a broader sense, using mold flow analysis insights with careful analysis of the simulation results enables engineers to streamline the manufacturing process when a part is ready for production.
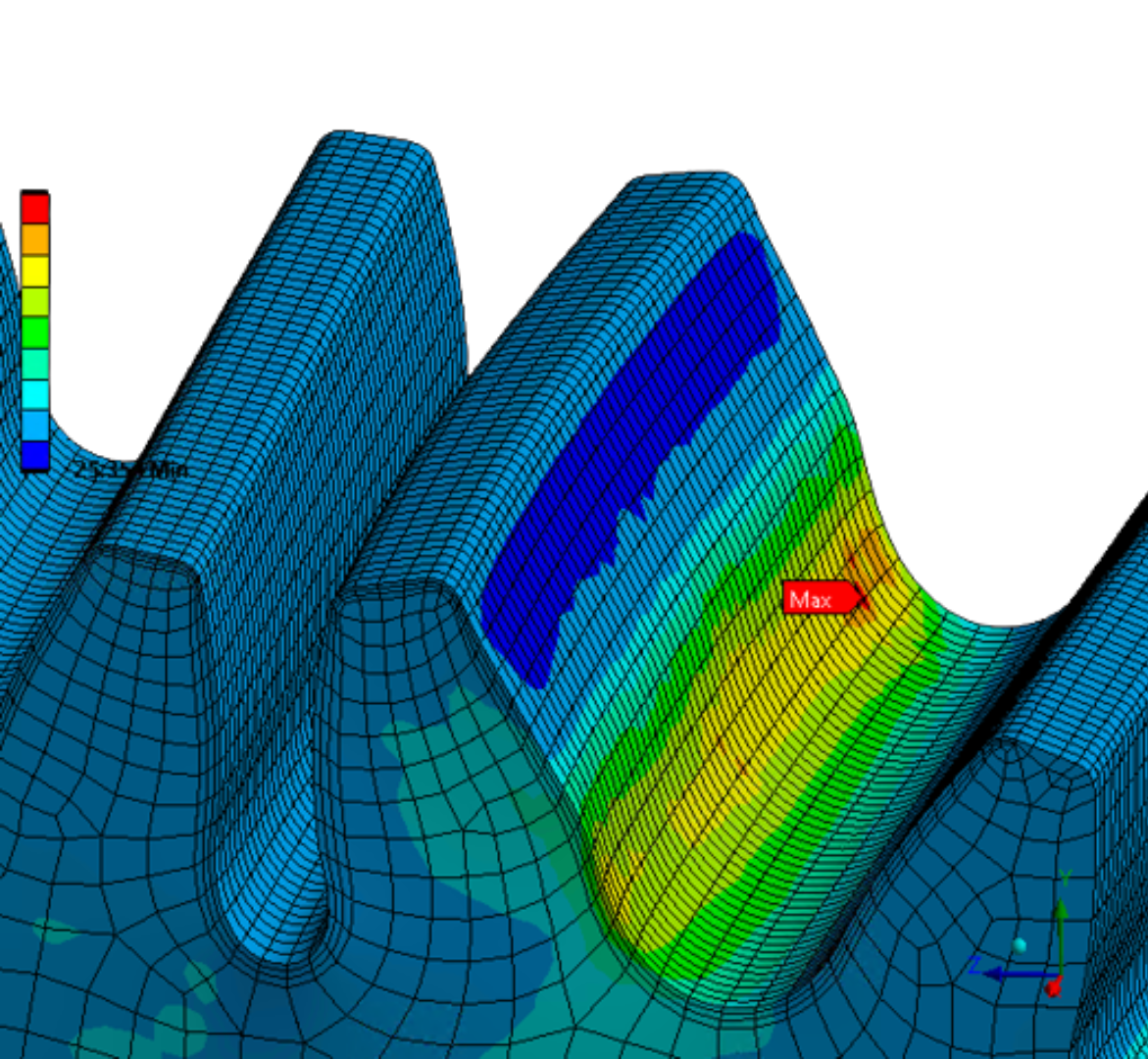
STRESS TEST WITH FINITE ELEMENT ANALYSIS
Not only do we use mold flow data for manufacturability, but when coupled with Finite Element Analysis (FEA), we can evaluate the true anisotropic performance of parts. Alpine has developed a workflow where the fiber orientation of a part is extracted from mold flow and used as a boundary condition for mechanical analysis. Evaluating the performance of components under their anisotropic material properties creates a high-fidelity analytical model before investing in a physical prototype.
OUR GOAL
With our unwavering dedication to engineering excellence and a strategic approach that harnesses the insights from our design for manufacturing approach, our goal is to deliver repeatable, easy to incorporate parts that satisfy all of your performance requirements.